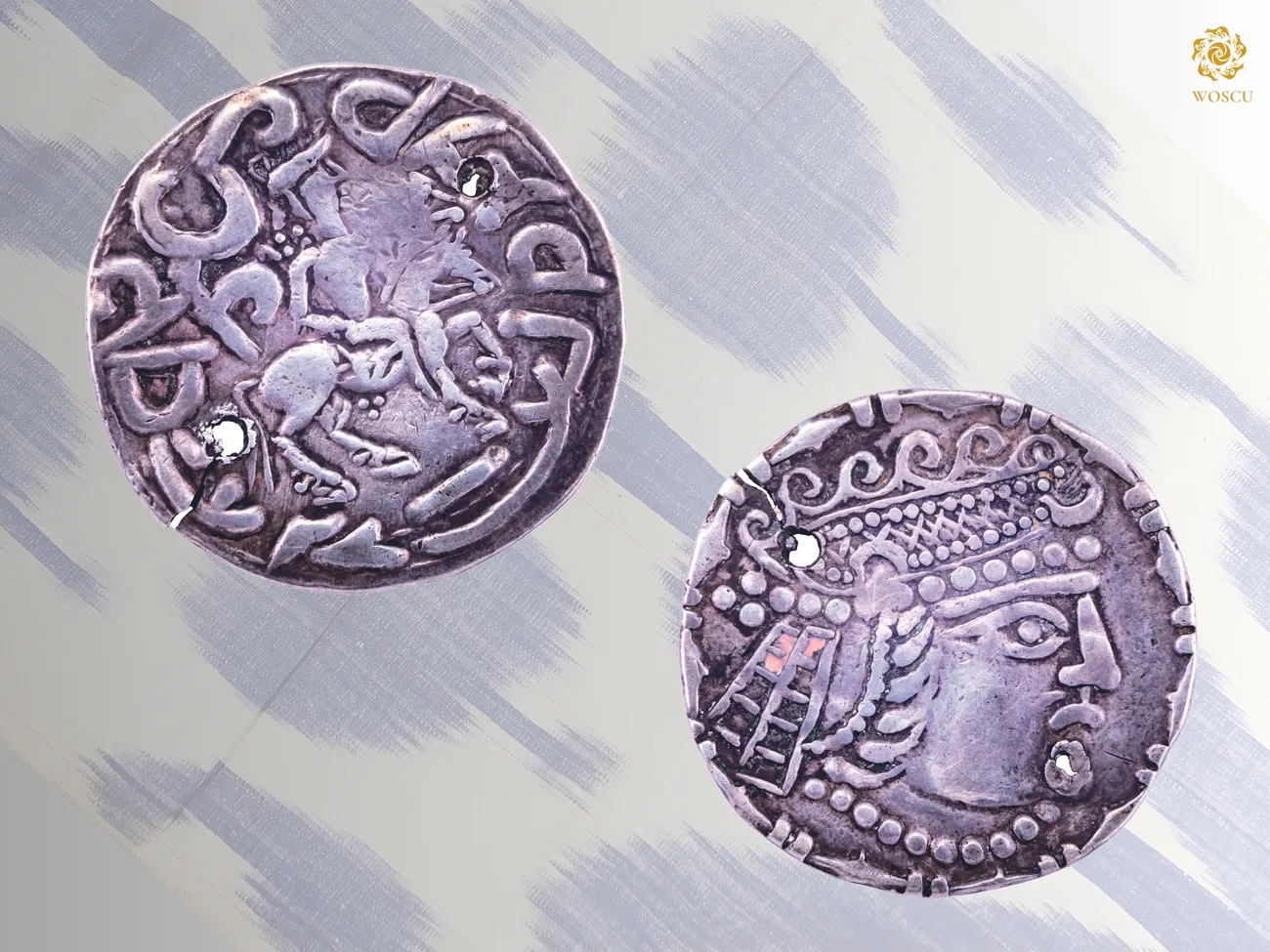
The main working tool in the manual minting, which remained in the Khiva Khanate until its last days, as well as during the existence of the Khorezm People’s Soviet Republic, is the coin stamp. This is the most important tool that determines the type of the future coin.
The stamps were manufactured by the engravers who worked at the mint. Having received the approved sketch of the image and the legend text of the future coin, they proceeded to make the minting tool. Two steel rods served as blanks for the stamp. The lower part of the stamp was fixed tightly. A coin blank prepared beforehand was placed on it. The upper part with the reverse side pattern was placed on the blank from above and held in place with tongs. After a strong hammer-stroke on the upper part of the stamp, a convex image was minted on both sides of the blank – the obverse and reverse of the future coin.
Finally, the coins were coated with wood oil in order to protect them from corrosion. After a certain type of coins was minted in sufficient quantity, the stamp was destroyed, thus preventing false-coiners from using it. To prolong the stamp’s service life, the apprentices warmed future coins up in the oven and fed them with tongs to the lower part of the stamp. Putting its upper part to a red-hot blank, the master struck the coin with a hammer.
Since the metal needed to stamp each coin was not weighed separately, the weight of each coin was slightly different. However, the total material consumption and the number of coins produced could be easily and accurately controlled.
You can learn more about the topic in the book-album "The Collection of the Ichan-Kala State Museum-Reserve" (Volume XLVII) in the series "Сultural legacy of Uzbekistan in the world collections".
The main sponsor of the project is the oilfield services company Eriell-Group.